Contingency Planning
October 18, 2019
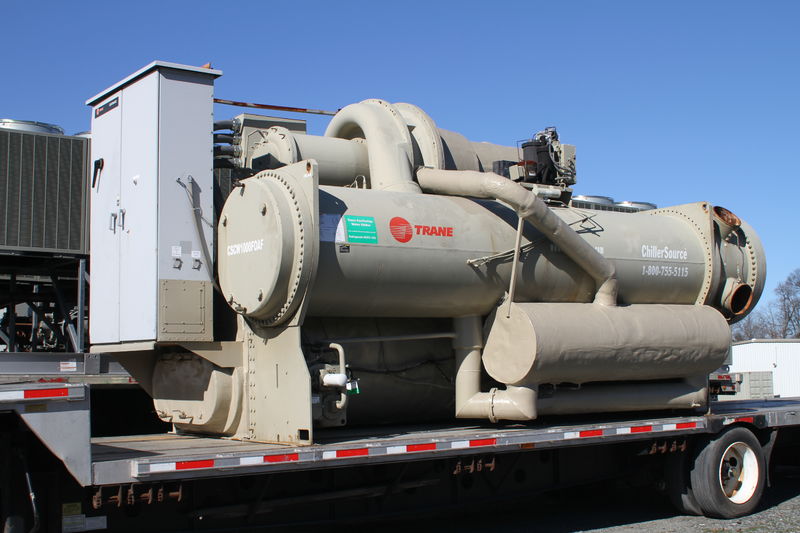
With Hurricane Isaac breathing down their necks on Aug. 28, 2012, administrators at a regional hospital in South Central Louisiana had plenty to occupy their minds. One thing they did not have to worry about was whether the storm would leave them without electric power or heating, ventilating and air conditioning (HVAC) services. If Isaac knocked the hospital off the local power grid, a rental generator was already on site to keep the lights burning, the HVAC running and lifesaving medical equipment working.
Because the hospital had a proactive power and HVAC contingency plan in place, the facilities management team was able to contact its temporary power and HVAC equipment partner and have the generator installed and ready to power the facility in about 24 hours.
No matter what industry you are in, it is critical to develop a power and HVAC contingency plan as part of a comprehensive crisis-response plan. Interruptions to power and HVAC – whether from a natural disaster or other challenges – can cause millions of dollars in damage, disrupt operations and erode stakeholder confidence. Developing an effective power and HVAC contingency plan minimizes financial risk, while protecting the health and safety of building occupants and providing peace of mind for an organization and its stakeholders.
Contingency planning is in fact so critical, that some insurance carriers require companies to produce a formal plan as a condition for providing business continuity coverage.
With all of this information, where do you start? Here are eight steps to consider when developing a contingency plan:
1. Analyze financial impact - Analyze the financial impact of a disruption in power or HVAC service. Experienced contingency service providers can help you estimate the true costs of unplanned downtime, which can go far beyond the cost of repairing equipment in a crisis mode. Additional unexpected expenses may include:
- lost finished goods or inventory
- reduced worker productivity
- diminished service levels
- lost customers or patients, and
- missed revenue or other business opportunities
2. Identify and rank potential risks – Determine the potential scope of system failures by identifying potential risks, including natural disasters, power outages, equipment failures or sabotage. Then rank them based on:
- their probability
- their potential to disrupt normal operations, and
- the accompanying financial cost
3. Evaluate mission-critical systems and address performance issues now - Perform a critical equipment audit that:
- Identifies mission-essential power and HVAC systems, and
- Assesses their current operating condition.
Use the results to address performance problems and document potential failure points. Companies tend to engage an energy services company (ESCO) or other third-party expert to conduct their audit.
4. Identify priorities and critical processes – Incorporate business priorities into the contingency plan to identify facility areas most critical to your essential operations and bottom line. This will make focus areas clear should an unplanned service interruption occur.
5. Determine equipment placement and connections – Seek out the best places to position temporary equipment on the site and know in advance how this equipment will connect to the building. This allows you to:
- Identify potential challenges
- prepare connection points in advance and
- arrange for any required permits
Additionally, take a moment to determine whether your current electrical service is sufficient to operate temporary equipment, such as a chilled water system or supplementary HVAC unit. When it comes to speedy response time during a crisis, there is no substitute for having the right connections for electrical, water and air ducts at the ready.
6. Compile results - Using the data gathered, develop a summary that outlines requirements, action steps, and associated costs and their allocation.
7. Confirm players on your team – Finalize the contingency plan and be ready for implementation if needed. Consider identifying a reliable, experienced partner – such as third-party contingency planning consultants, temporary equipment providers, or combinations of the two – to help develop and implement an effective power and HVAC contingency plan.
Top HVAC industry contingency planning consultants offer proven tools to ensure that your organization develops a complete, effective and useful contingency plan ready for application. To find a leading consultant, look for large equipment inventories, conveniently placed locations, and a proven track record showcasing world-class response time and a reputation for high customer service levels.
8. Practice, practice, practice - Assign roles and responsibilities and provide training.
- Conduct drills to verify the contingency process and identify areas for improvement
- Make required building modifications in advance
- Update the plan annually or in conjunction with a significant facility change, such as a building modification or expansion
Investing time and money on contingency planning can pay for itself several times during its first use. In fact, maintaining an effective, well-understood and broadly shared contingency plan can pay off in many ways. It enables a company to:
- minimize service interruptions
- reduce capital loss,
- maintain or restore normal operations sooner
A contingency plan is a necessary tool to keep in your toolbox. It creates peace of mind for the business, its customers, employees and other stakeholders.