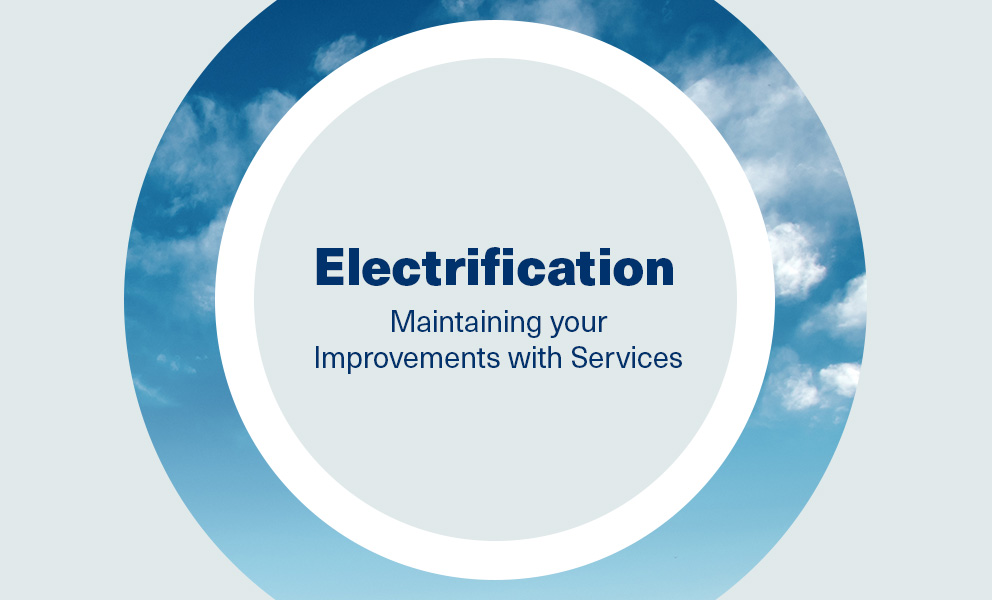
Insights from an Expert: How you can Efficiently Heat and Cool your Building While Meeting Decarbonization Goals
Part 1 reviewed electrified HVAC equipment and system design/selection; part 2 considered funding mechanisms for electrification projects via energy services and controls. In today’s discussion, we dig into how HVAC Building Services and Intelligent Services are a critical piece of any customer’s sustainability story.
Q. What are the challenges customers are facing with upgrading to electric HVAC systems?
A. The first thing is the lack of digital infrastructure and accurate data to help them assess and make good decisions on how these systems are going to perform in their building with their existing infrastructure. Data is necessary to know how to most economically select and apply this equipment.
Q. For customers just starting their decarbonization journey and considering a move to an electric system, is there anything they can do with the system they have?
A. So, what we’ve said to many of our clients is: “You don’t have to completely electrify all at once. Let's keep efficiency at the forefront, because having your building operate efficiently will give you decarbonization benefits—reducing electricity, reducing gas and reducing district steam is inherently decarbonization. And while we're doing that, let's make sure we're putting in smart systems so that you have the data to collect, analyze and optimize your building starting now, and so that you’ll be able to make intelligent capital project decisions in the future.”
Q. How does regular maintenance help achieve this “start small but smart” approach?
A. Regular maintenance is key to catching inefficiencies early. It’s not uncommon to find that an operator in the field has created a makeshift “fix” to solve an immediate issue. But if we were to dig in first, we could find more strategic solutions for the immediate issue that don’t negatively impact overall energy usage. The goal to regular maintenance as a means to electrify heating and cooling is to identify ways to use as little energy as possible, as efficiently as possible. It’s critical that everything is optimally run and controlled.
And then of course it helps reduce unplanned downtime. I saw an air handling unit today that clearly hadn't been maintained for a very long time. They shut it down so I could look inside. The fan wheel was clogged with dust and dirt. There was no airflow going through that fan, and it was running as hard as it could to try to deliver cold air to the space. Over time, mechanical pieces fail. Bits of dirt and debris get caught in different types of systems, like fan systems and air systems. Water systems can also develop various types of buildup that cause inefficient flow. Just by shutting the system down every three months and cleaning the dirt out of it, you get improved airflow and better efficiency. These are just basic things, you know.
Q. I’m hearing you say that catching things early is key—I can’t help but wonder then about preventative maintenance?
A. Preventative maintenance is really important. Without it, you’re waiting for there to be an issue and then addressing it—while regular maintenance can catch it, and early preventative maintenance can avoid it altogether. That’s really where Trane’s Intelligent Services come in. Building owners may know what their equipment is doing when they must conduct maintenance on it, but they might not know what’s going on with it in between servicing. With data from remote monitoring, they can be more proactive and understand if something is about to break three months before their next planned maintenance. They can address it before it fails. Remote monitoring can also help with energy trending data—watching what is happening 24/7 can give insights into places where the system can be further optimized.
For example, I know of a project where through analytics and energy tracking, we found out that a school’s energy profile was spiking mid-day, and after investigating, it was found that kitchen equipment, all the lights and the HVAC were running at the same time. By shifting when the industrial dishwasher was run, the whole building ran on less energy—there wasn’t a “problem” per se—no one was complaining. We just used the data to be proactive. Finding energy inefficiencies and working to solve those is how you create a more sustainable building overall.
The other key to proactive maintenance and service is that it provides peace of mind. For many customers, we hear concerns about the reliability of all-electric heat: “Will this keep my building warm in the middle of winter? What about the rolling brownouts we have in the summer, could that happen in January?” What I often share with customers who have these concerns is that we can use remote monitoring and service to make sure that the equipment is always up and always on (true for non-electric equipment too). But even better, we can couple that with controls strategies and auxiliary heat. So, if we notice something that may be cause for concern, we can shift the way the building is being heated before anyone even feels cold.
Q. When it comes to maintaining and optimizing HVAC equipment to support decarbonization goals, how important are Trane's Intelligent Services?
A. I think it’s paramount, quite honestly. I had a client for a number of years with an industrial building. They could only plan maintenance twice a year, so they had to get by for six months at a time. And they never knew when something was about to break. If it broke, it was an urgent failure. They had to pull 24-hour shifts to get it back up in operation. And they lost hundreds of thousands or millions of dollars per day that their process was down. They didn’t have monitoring controls on a lot of their equipment.
So, we went on to tell them, "Hey, if you’re worried about downtime on your process equipment, wouldn’t it make sense to put some monitoring devices on your conveyor belts and fan motors? That way, as soon as they start getting out of whack, you can take them offline to fix when it’s convenient, rather than just waiting for them to break. Because when a bearing breaks, it then breaks the shaft, which then messes up the motor, which then tears a belt. Now you’ve got a much bigger problem.”
That’s just a small example. The same thing applies to a large HVAC system. There’s plenty of data delivered by Trane equipment that can tell you not just whether it’s operating, but also its efficiency health. We can provide our clients with regular reports, and if something pops up, we’ll drop a note and say, “Hey, you may want to check out this thing we noticed.” And they’ll say, “Oh wow, my outside air damper was stuck open. I greased it and now it’s working properly.” When it’s 95 degrees and humid, that’s a lot of energy they lost if their outside air damper was stuck open instead of it being at the minimum ventilation position. So those types of controls and insights are paramount to maintaining buildings and understanding where you focus.
Q. Beyond regular maintenance, what’s the best thing Trane can do to set up customers’ bigger decarbonization work? What’s the right thing for their building today that also sets them up for tomorrow?
A. It's doing what we've always done—focusing on helping buildings be more efficient upfront, whether that's doing preventative maintenance or focusing on smarter controls or deploying energy conservation measures with existing equipment.
When I approach a customer, it starts with discovery, “What are your goals? What data do you (or don't you) have that can help us understand what's happening?” Most people need a financial return on larger scale projects. When I hear that, I say, “Let’s set you up for meeting decarbonization goals by looking at efficiency projects first.” In most buildings there’s an opportunity to replace or address some wish list items—controls, lighting, maybe window films, a little envelope work. It just depends on the building and what their goals are.
Whether or not decarbonization is a prevalent thought in the client’s market and something they talk about all the time, our approach is the same. We go in, learn what our customer’s problems are, and we try to help fix them.
Q. What should building owners look for when they're selecting a services partner that can support electrification and decarbonization goals?
A. As much as we’d want to say look for whoever has the most technical knowledge, it's really about the people. When I have relationship with a customer, I’m going to research the things that I know they find important, and we're going to have conversations about those things. For the most part, clients choose a services provider because of their approach to people—how they communicate, and whether they trust that they know what they're doing and they're giving good, unbiased advice. They’re not just trying to sway me because they're selling it.
Electrification of Heat Solutions

About the Author
Corey Letcher, Trane Complex Solutions Account Executive
Corey Letcher helps clients solve unique challenges related to energy, energy conservation and the economic impact sustainability has on businesses in various vertical markets. His track record includes helping businesses identify and execute projects to address these challenges through efficient (re)design, creative energy procurement, energy conservation management and, more recently, decarbonization. He also has experience evaluating and deploying creative financing and creative thinking to generate revenue from the projects to help them align with clients' specific business goals and metrics.