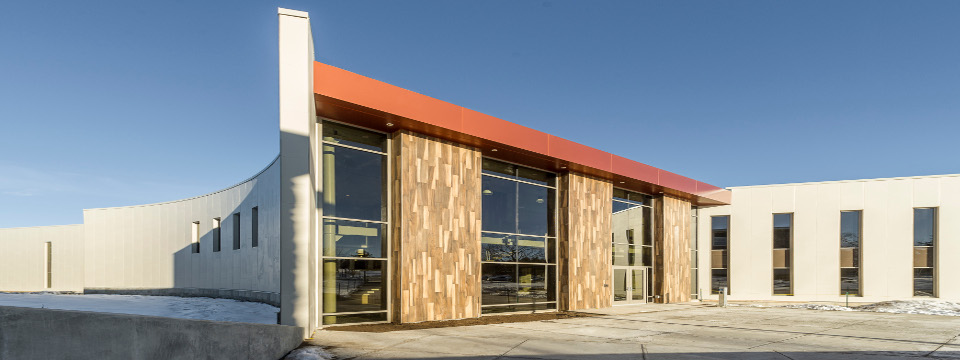
Challenge
In March of 2012, JCC signed the American College & University Presidents Climate Commitment (ACUPCC) to promote campus and community awareness of global warming issues and develop ways to mitigate their effects. In line with its commitment, JCC completed baseline greenhouse gas emissions reports, which showed that about 14 percent of the JCC carbon footprint is from on-site combustion (natural gas), 15 percent is from purchased electricity, and 71 percent from student, faculty and staff commuting. A Facilities Master Plan was developed to serve as guidance for campus improvements. With a target date of 2050 to reach net zero carbon emissions, JCC implemented a Climate Action Plan to evaluate opportunities in terms of their total greenhouse gas reduction, their feasibility, financial costs and savings derived.
A history of sustainability and partnership
Over the years, JCC has made strides in energy management, conservation and recycling. Efforts have included educating the campus community on energy wasting behaviors, providing hands-on learning opportunities, and implementing initiatives of its EverGREEN Committee, which spearheads campus sustainability efforts. Campus upgrades have included the addition of thermal storage, sub-metering to obtain energy data, and a high-efficiency boiler; as well as implementation of direct digital controls to more efficiently manage its systems.
A long-range action plan
The Phase I goal of JCC’s long-range Climate Action Plan is to reduce energy use by 1 percent per year. The primary targets include reducing commuter miles through incentives, use of alternative transportation and the increased availability of on-line classes; and improving building envelope and energy management strategies. Phase 2 will pursue a steady course aimed at reducing CO2 equivalent by 200 metric tons annually, focusing on vehicle emissions, renewable energy and new technologies. JCC knows that a sustainable Climate Action Plan will require an ongoing commitment from a variety of stakeholders, strategic financial investments, and periodic re-assessments to take advantage of new opportunities.
Solution
When JCC began planning construction of its new 36,958 sq ft John W. Deans Collaborative Learning Center, the college turned to its long-term partner, Trane, for assistance. JCC sought an energy efficient solution that would provide capacity to cool the new learning center and add air conditioning to the adjacent David G. Gregor Building, without incurring a large increase in operating costs.
Managing peak demand
Pleased with the operation and energy efficiency of its previously-installed EarthWise™ Ice-Enhanced Air-Cooled Chiller Plant, JCC selected the same system for the new learning center. The thermal storage plant leverages high efficiency HVAC equipment and advanced building controls in a complete design concept that optimizes performance. Tapping into the collective capabilities of pre-programmed controls and a pre-engineered system package reduces risk, complexity and costs. The system includes a Trane 90-ton CGAM air-cooled scroll chiller, used in conjunction with four CALMAC IceBank® thermal energy storage tanks. The system builds ice at night when the building load is low, taking advantage of lower-cost, off-peak electricity. During the day, the ice and the chiller work together to cool the facilities.
Optimizing performance
Building operators use a Tracer™ SC controller to manage the EarthWise System. With a click of a button, facility managers can monitor equipment, make set-point changes, manage alarms and decide whether to melt, make or preserve ice. Tracer SC dashboard screens make reporting and programming adjustments simple, using a workstation or with remote access via a Web-connected device, such as a smartphone or tablet.
Results
Installation of a Trane EarthWise Ice-Enhanced Air-Cooled Chiller Plant to serve its new John W. Deans Collaborative Learning Center and existing David G. Gregor Building has enabled JCC to shift 150 KW of peak energy demand usage to less expensive nighttime hours, helping to reduce energy costs, manage peak demand, and take advantage of lower cost offpeak electricity. The new chiller plant, located in the center of campus, also provided JCC the opportunity to create a teaching station by adding signage to explain the sustainability benefits of thermal energy. “We are building momentum as we work toward our ACUPCC goals,” said Bruce Alexander, Director of Facilities, Jefferson Community College. “As we continue to implement energy efficiency improvements, we are also increasing environmental awareness among our students, and the success of one project is making it easier to get approval for the next one.”