Project Highlights
Location: Farmington, Maine
Industry: Higher Education
Products Used: Controls, Energy Storage
Services Used: Energy Supply, Energy Efficiency Contracting, Upgrading
Climate: Dry & Cold
Topic: Sustainability, Innovation, Efficiency, Cost-Saving, Decarbonization, Energy Services, Products and Solutions, Solar
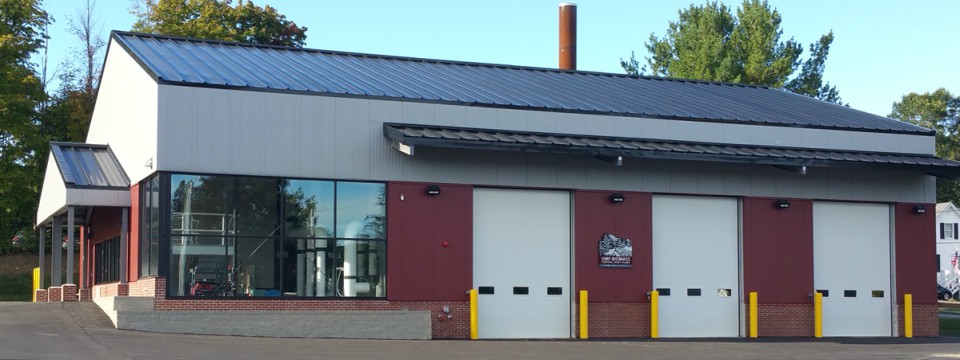
Farmington, Maine
Challenge
As the 150 year old University of Maine System acquired additional buildings to accommodate the growth on each of its seven campuses, its infrastructure also grew. In the case of the University of Maine at Farmington, its campus grew to include thirty-five buildings on a sprawling campus served by many independent mechanical plants and heating systems. Many of the aging mechanical systems were failing, and had become costly and time-consuming to maintain and operate. Wishing to improve system reliability, combat the high costs of heating, and work toward its commitment of becoming carbon-neutral by 2035, UMF took action, issuing a Request for Proposal (RFP) to obtain conceptual approaches to meet its challenges. “Our RFP was a little vague on purpose,” said Kate Foster, president, University of Maine Farmington (UMF). "We wanted a fresh look at our energy use and to see what system alternatives were available.”
Solution
Trane developed and delivered the design-build solution. To do so, the local Energy Services and Contracting Team led the effort and managed all aspects of the design-build contract including engineering, sub-contractor selection, equipment procurement, project management, site safety, and ultimately system commissioning, warranty administration and on-going maintenance and service activities.
Replacing boiler system with central biomass heating
Nearly twenty-two buildings had their existing boiler plants replaced through connection to the new 5,885 sq ft Central Biomass Heating Plant designed with built-in redundancy to handle tough Maine winters. Using a renewable, locally-sourced fuel, the central biomass heating plant contains a 500 HP solid fuel wood chip boiler with a full-capacity LP gas burner for 100 percent backup of the biomass system. The largest biomass hot water heating plant in the State of Maine, the plant can burn two tons of chips per hour under full load. Supplied by fifty miles of highly forested land surrounding the campus, the biomass fuel storage bunker has the capacity to store up to 120 tons of wood chips that can provide heat to the campus for up to three days at full capacity. If needed, the backup propane storage tank can supply an additional two days of capacity.
The central plant is connected to the campus buildings using a high tech, underground hot water distribution system. The system includes approximately two miles of super-insulated steel piping that delivers 210° water to heat twenty-two of the largest buildings on campus, offsetting 95 percent of the fossil fuel used.
Improving efficiency with integrated controls
The twenty-two buildings served by the central plant have been integrated into the Trane Tracer® Ensemble™ building management system. The fully automated system enables UMF facilities personnel to monitor real-time energy usage in the biomass plant and control equipment in all of the connected buildings on campus. “We didn’t have central control before,” said Jeff McKay, director of facilities, UMF. “With Tracer Ensemble, all of our systems talk to each other. It’s visible, we can fix problems more efficiently, and we are using less energy.”
Results
Exceeding its self-imposed sustainability goals committed to in the President’s Climate Commitment, UMF took a huge step toward becoming fossil-fuel free, working with Trane to add a biomass heating plant to its campus. The new biomass plant is outperforming expectations in its first year of operation, lowering energy usage and costs, while improving reliability and reducing maintenance costs through the upgrade or replacement of aging mechanical infrastructure. A payback on the project is expected in less than 10 years.
The UMF plant has eliminated the consumption of 390,000 gallons of no. 2 oil, or 95 percent of the prior fuel usage, with locally sourced, sustainable wood biomass. Twenty-two campus buildings are now heated with about 4,500 tons of hardwood chips per year, decreasing the University’s carbon emissions by 4,000 tons per year. The wood chips used in the biomass heating plant are sourced within fifty miles of campus, creating jobs to help the local economy and providing a boon for the area by generating $7 in economic activity for every dollar spent to fuel the plant.
“We’re saving money by not having to purchase other energy, and our output is ahead of where we thought we would be,” said McKay. “We are able to pay for the new plant with the money we are saving,” added Laurie Gardner, executive director for finance and administration, UMF. “Once it is paid for, the university will have funds to direct toward other student benefits.”
Besides heat, UMF is using the plant as a learning facility where students can actively engage in understanding biomass energy, associated systems and processes. Biomass energy will also be embedded in several courses as a mandatory learning facet of several curricula and fields of study. The plant control room is open for tours for area students and other visitors, allowing them to view the internal operations through several exterior viewing areas. “I like to compare it to a Goldberg machine you might see at a science museum,” said Gardner. “It’s a learning tool that is intriguing for visitors to watch.”
“The biomass central heating plant is proving to be taxpayer dollars well spent,” said Foster. “It’s definitely something to be proud of.”
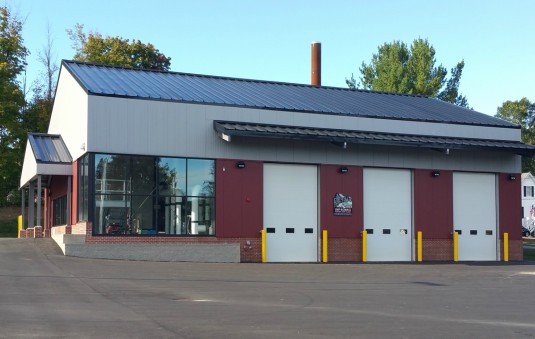