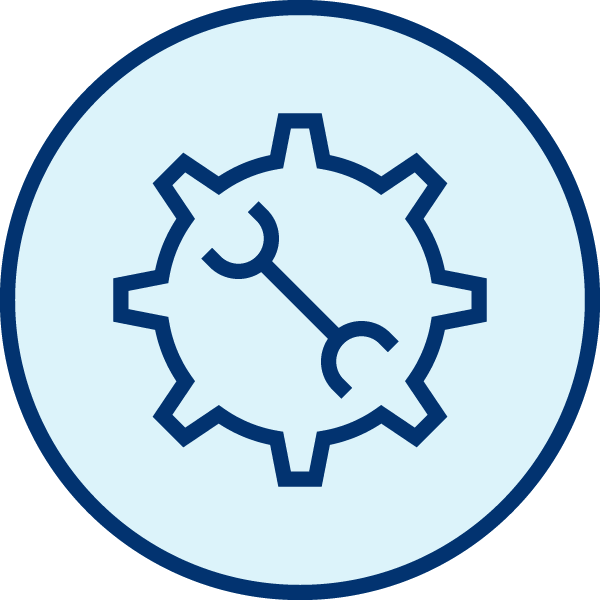
Make technician visits one and done.
An area is too hot, the space is clammy—so you call for service. In a non-connected building, technicians arrive without any insight into the root cause or the right parts in the truck to address the issue. Connected controls enable technicians to complete first-pass diagnostics and troubleshooting remotely and arrive fully prepared to make a repair.
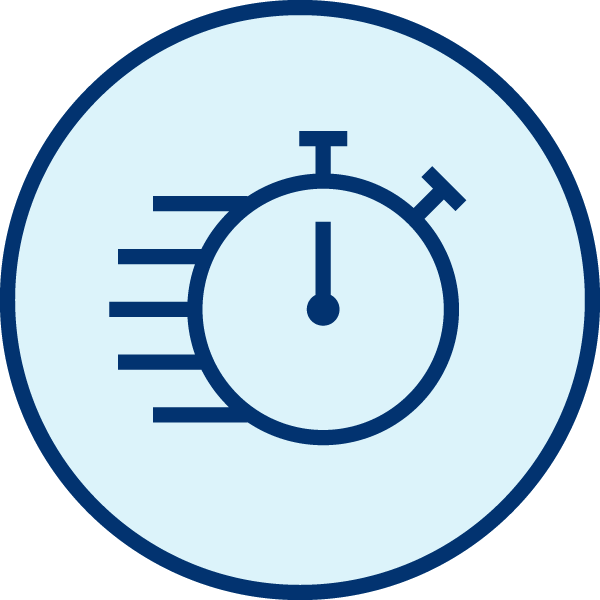
Save on after-hours service fees
After-hours emergency service is expensive. With connected controls and solutions, each alarm can tell you the level of urgency. You’ll know if the event needs immediate attention, can safely wait until standard business hours, or best case can be managed remotely without requiring a service visit at all.
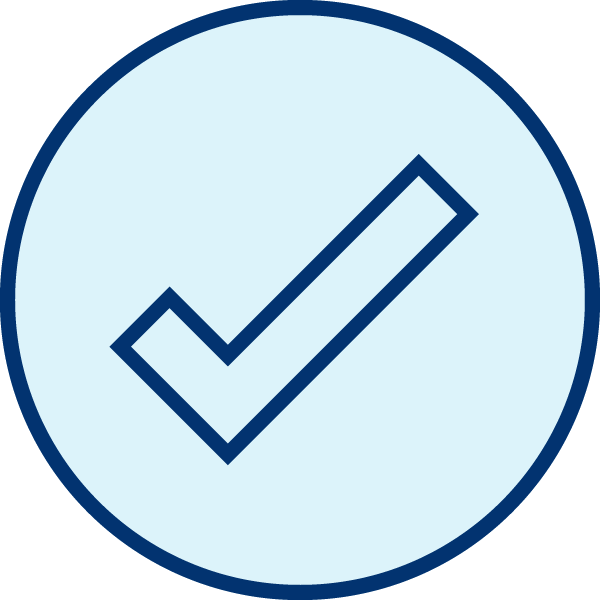
Do it yourself
In some non-connected buildings, virtually every adjustment and schedule change can require third-party service support—and fees. Connected controls and solutions allow building mangers, administrators and even occupants to make simple changes (with guardrails to prevent major errors).
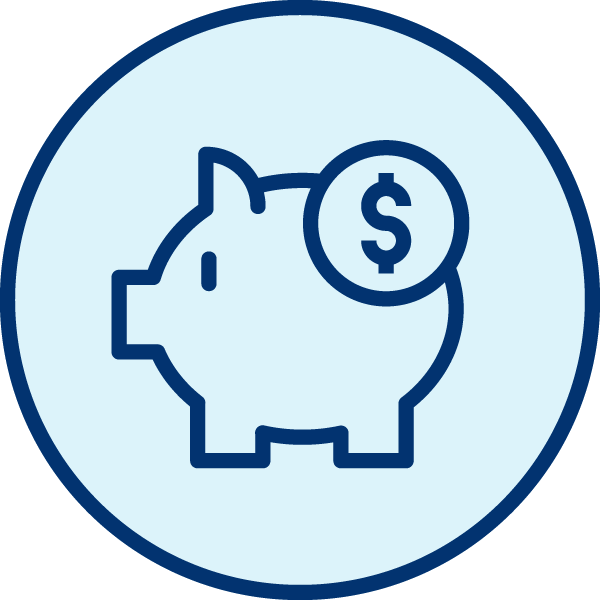
Maximize your equipment investment
Equipment that falls out of spec leads to excessive wear and tear, and potentially premature failure. Remote monitoring helps prevent an unplanned financial burden and squeezes more value from your investment.
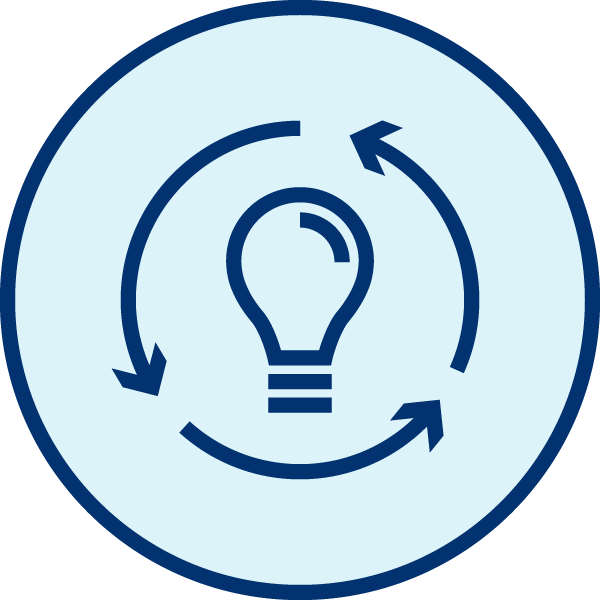
Optimize energy use
Buildings without connected “smart” controls can waste money by inadvertently running with overrides, sticking to inflexible schedules that don’t align with occupancy and other inefficiencies. By optimizing building operations with connected controls, your HVAC uses only the amount of energy that’s really needed.
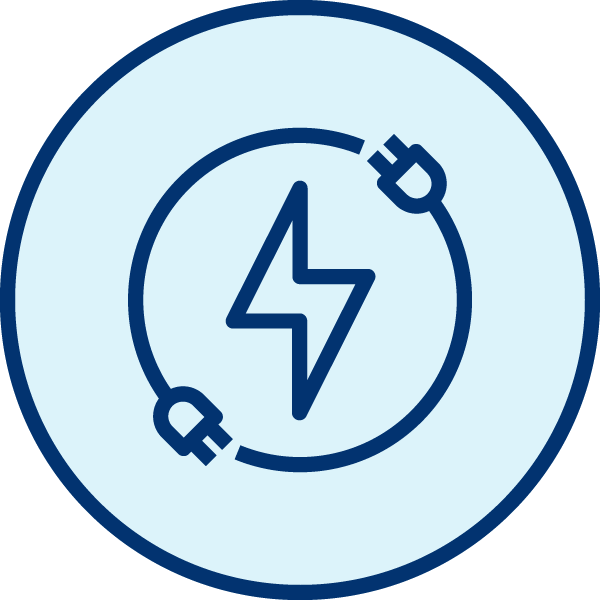
Align sustainability with profitability
In some areas, energy prices rise when demand is highest. If you can shift energy use to off-peak times you can take advantage of lower rates and save significantly. You can make that happen through equipment cycling, demand management and thermal storage, all controlled through a building automation system.
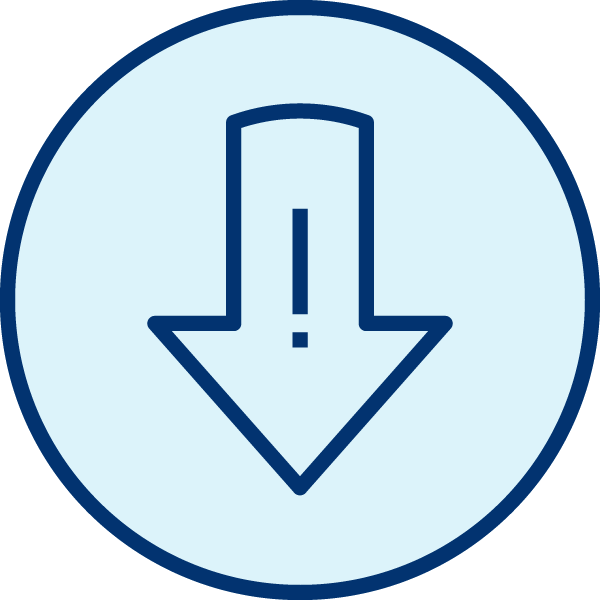
Prevent unplanned downtime
Unplanned downtime may be one of the greatest HVAC-related costs. In data centers, servers and equipment can be damaged from overheating. In manufacturing plants, lost productivity means lost revenue. Hospitals may incur compliance fines. Predictive analytics, smart service scheduling and 24/7 remote monitoring reduce the likelihood of downtime.
Related Content
-
Crosstown Concourse Customer Story
Collaborative effort delivers effective HVAC, controls, and energy management solutions to increase asset potential; helps realize $250,000+ in capital first cost savings and reduced life cycle costs of $1.3 million+; assists vertical urban village in becoming catalyst for growth.