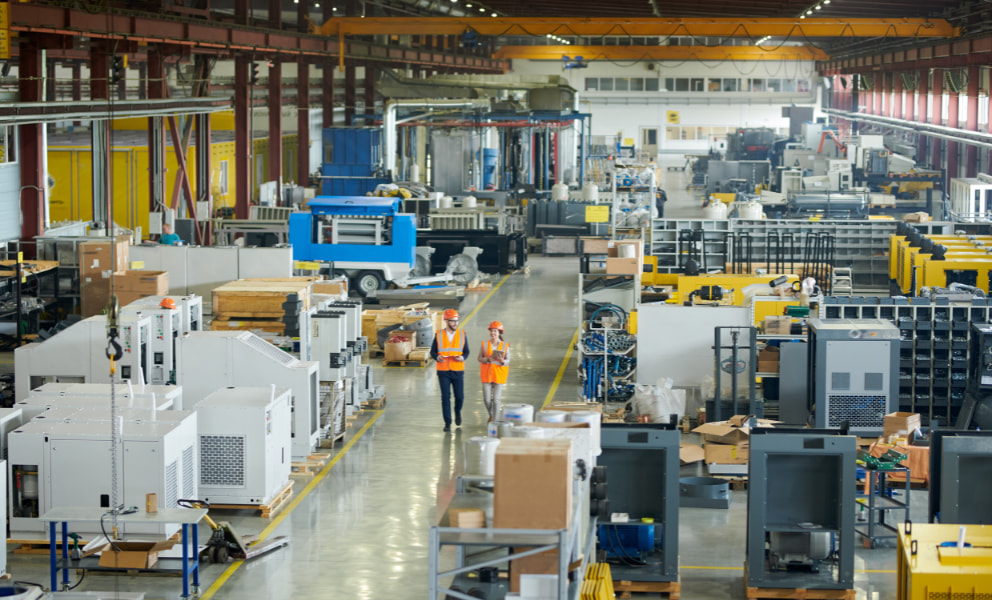
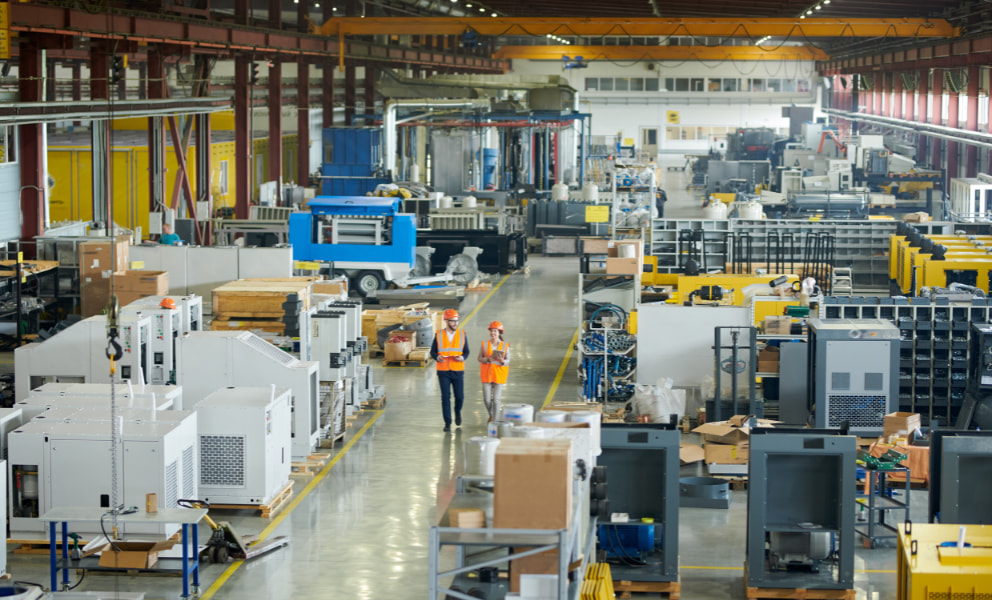
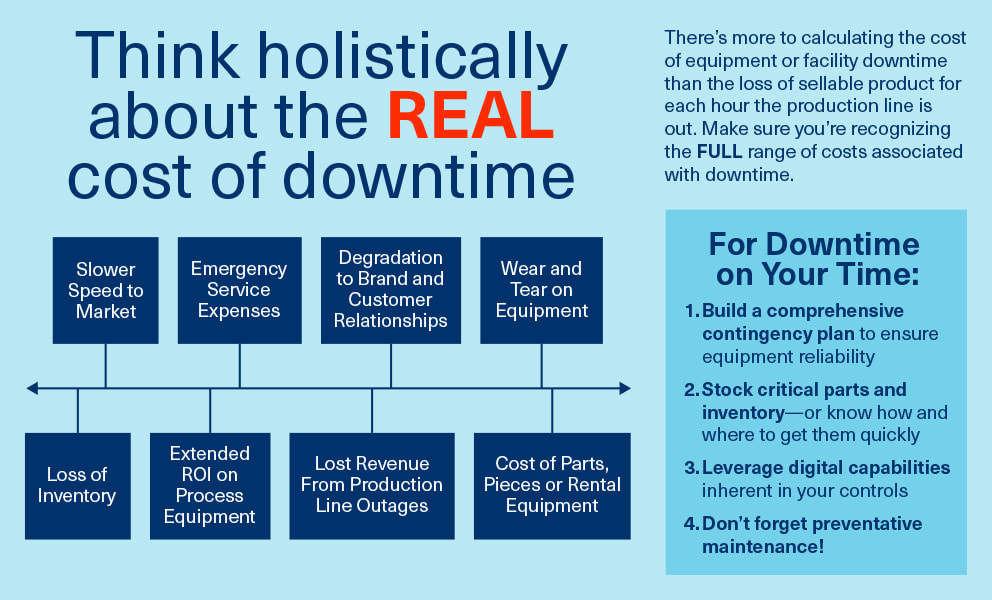
Lorsque nous discutons avec les fabricants des coûts potentiels des temps d’arrêt, nous entendons régulièrement qu’il est difficile de quantifier tous les composants qui entrent en ligne de compte dans le coût réel des temps d’arrêt. Il y a trois coûts évidents que la plupart des entreprises prennent en compte et peuvent facilement calculer :
- Perte de revenus en cas de panne des lignes de production et/ou perte de stock lorsque le produit doit être refait. Une ligne qui ne fonctionne pas ne gagne pas d’argent – cela peut représenter jusqu’à 6 à 7 chiffres de perte de revenus pour chaque jour de panne de ligne. Mais même lorsque toutes vos lignes fonctionnent, les variations des conditions ambiantes peuvent rendre le produit inutilisable. Dans la production de gélules, par exemple, la marge d’erreur dans la gestion des conditions de fabrication ambiantes est très mince, de sorte que la moindre variation peut entraîner la détérioration du produit et une perte de stock. Ou, dans une entreprise d’embouteillage, où les bouteilles en plastique ne peuvent pas être remplies tant qu’elles ne sont pas correctement refroidies, en cas de panne dans ce processus de refroidissement, la production de stocks s’arrête complètement.
- Les frais de service d’urgence associés au coût de l’intervention d’un technicien pour réparer le produit. Si l’équipement tombe en panne un soir ou une fin de semaine, des tarifs de service plus élevés peuvent s’appliquer. De plus, le technicien que vous obtenez à court préavis peut ou non connaître votre installation ou votre équipement et peut donc prendre plus de temps pour résoudre le problème.
- Coût des pièces, des pièces ou de la location d’équipement pour un équipement qui est irréparable sur place. Il peut être nécessaire de commander de nouvelles pièces et de louer de l’équipement pour que la production provisoire puisse reprendre. Et des frais d’expédition urgente peuvent être encourus si les bonnes pièces ne sont pas en main.
Beaucoup comptent sur le total des factures reçues (pour le service, les pièces ou les locations, le nouvel équipement, etc.) et sur la combinaison de cela avec la valeur marchande de la capacité et de la production de leur chaîne de production, et la perte correspondante de produit vendable pour chaque heure de panne de la chaîne. Mais, en réalité, de nombreux autres coûts entrent en jeu lorsque des temps d’arrêt se produisent.
Un calcul exact des coûts des temps d’arrêt doit inclure les éléments suivants :
- Usure de l’équipement lorsque la défaillance se produit. Cela peut affecter non seulement la pièce ou l’équipement défectueux, mais également d’autres équipements connexes dans le processus. Dans certains environnements, les gros moteurs et les salles de contrôle doivent être refroidis de manière très spécifique. Si ces espaces ne peuvent pas être correctement refroidis, l’ensemble du système peut devoir être arrêté, ce qui entraîne une pression supplémentaire sur le système lorsque tout est remis en marche.
- Coût d’opportunité d’une vitesse de mise sur le marché plus lente. Si le produit n’entre pas sur le marché, les bénéfices seront sacrifiés. Dans l’industrie des véhicules électriques (VE), par exemple, la rapidité de mise sur le marché représente un énorme avantage concurrentiel. Votre produit doit être disponible pour que les clients puissent l’acheter. La course pour être le « premier » avec n’importe quel type de véhicule électrique fait la différence entre être en tête ou être un suiveur rapide.
- Un retour sur investissement plus lent sur les équipements de traitement, en particulier pour les achats d’équipements d’équipement plus coûteux et plus technologiques. L’augmentation des temps d’arrêt et la baisse de la production signifient que le délai pour atteindre l’équilibre de vos investissements en capital sera prolongé.
- Dégradation de la marque, de la réputation et des relations avec les clients. La perception de votre capacité à livrer des produits à temps et de haute qualité peut en souffrir. Pour les fabricants de niche, vendre à seulement quelques grands acteurs, comme la plupart des acteurs de l’industrie pharmaceutique, un « mauvais travail » peut être préjudiciable.
Ainsi, plutôt que de faire un examen après le jeu du coût réel des temps d’arrêt, comment pouvez-vous optimiser votre capacité à maximiser le temps de fonctionnement ?
1. Élaborez un plan d’urgence complet qui garantit la fiabilité de votre équipement et de vos processus afin d’éviter des temps d’arrêt coûteux. Il s’agit notamment de connaître votre partenaire de location avant que votre équipement ne tombe en panne et de savoir comment vous allez puiser dans l’électricité, l’eau, les vannes, etc. Il doit également inclure tous les schémas critiques de l’usine, les informations clés sur les stratégies et les calendriers de contrôle et toute autre information pertinente nécessaire à l’équipe qui vous remettra en service. Avec une flotte robuste de techniciens et d’équipements stationnés dans tout le pays et des décennies d’expérience dans le déploiement de solutions CVC OEM temporaires, Trane Rental Services peut vous aider à élaborer un plan d’urgence complet et l’exécuter rapidement en cas de défaillance de l’équipement ou pour une maintenance planifiée.
2. Stockez les pièces critiques et l’inventaire. Ou savoir comment et où les obtenir rapidement en cas d’urgence. Cela permettra d’éviter les problèmes de chaîne d’approvisionnement qui peuvent survenir lorsqu’une pièce critique est nécessaire de toute urgence. Savoir quand et où intégrer des redondances dans vos processus et équipements peut également vous aider à éviter des problèmes majeurs. Notre analyse approfondie des services de location vous assurera d’être couvert.
3. Tirez parti des capacités numériques inhérentes à vos contrôles. L’utilisation de commandes numériques peut fournir des données en temps réel pour aider à surveiller les conditions ambiantes et l’état de l’équipement dans l’ensemble de vos installations. L’utilisation de modèles numériques et d’IA peut vous aider à anticiper les problèmes avant qu’ils ne surviennent et à résoudre les défaillances futures avant qu’elles n’entraînent des temps d’arrêt.
4. N’oubliez pas l’entretien préventif. Le plan doit inclure des stratégies d’entretien régulier et préventif afin d’éviter complètement les crises. Si vous savez qu’une pièce d’équipement est susceptible de tomber en panne au cours d’un certain mois, vous pouvez planifier une maintenance mineure le mois précédant un incident majeur. Votre plan d’urgence pour la location de Trane s’occupera de ce scénario. De plus, le passage à un modèle de maintenance plus prédictive qui exploite les données cloud, les logiciels et les outils d’analyse peut aider à surveiller en permanence votre installation afin d’être en mesure de repérer les problèmes avant qu’ils ne deviennent des problèmes majeurs, ce qui vous permet de gérer les temps d’arrêt à votre rythme. L’équipement de location de Trane est doté de capacités de surveillance numérique à distance pour vous donner un aperçu transparent de votre équipement et permettre à notre équipe d’ingénieurs d’intervenir 24 heures sur 24 et 7 jours sur 7 avant que les temps d’arrêt ne deviennent des heures de pointe.
De nombreux facteurs doivent être pris en compte pour minimiser les temps d’arrêt, et il est important d’avoir des plans d’urgence qui sont mis à jour en fonction des conditions actuelles du marché, des progrès technologiques et des nouvelles meilleures pratiques de l’industrie.
Trane est un conseiller de confiance qui peut vous aider à planifier l’ensemble du cycle de vie de vos équipements et installations. En plus de nos offres robustes d’ingénierie et d’équipement de location, nous vous accompagnons dans votre parcours pour vous conseiller sur tous les éléments de vos installations : vente d’équipement et service continu, contrôles et surveillance, maintenance prédictive, soutien aux données et aux analyses, et notre réseau inégalé de fournisseurs d’équipement et de services. Peu importe où vous en êtes dans votre voyage, commençons !