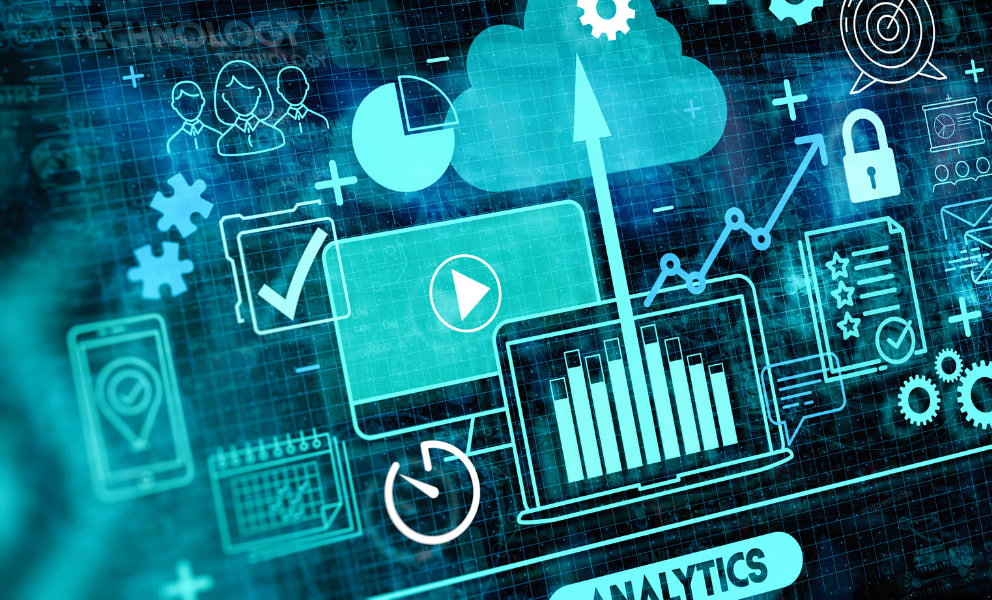
L’industrie 4.0 est là et change radicalement la façon dont les installations industrielles sont gérées. Tout comme nos montres ont évolué, passant de l’indication de l’heure et du comptage des pas à l’envoi de messages texte, à la mesure de notre fréquence cardiaque et de l’exercice et à la fourniture de mises à jour météorologiques, l’entretien et la gestion des bâtiments ont également évolué de manière significative. De nouveaux produits et technologies sont intégrés dans les installations de production et dans l’ensemble de l’exploitation des bâtiments.
Alors que de nombreux secteurs sont confrontés à des changements radicaux dans la plupart des facettes de leurs opérations, les organisations de premier plan ne veulent pas seulement se transformer, mais savent aussi qu’elles DOIVENT se transformer pour rester pertinentes. Et ils doivent le faire de toute urgence. Cependant, elles constatent souvent que leur transformation vers l’industrie 4.0 est plus lente que prévu et ne donne pas toujours les résultats escomptés.
Pour les entreprises du secteur des sciences de la vie, un contrôle strict de l’environnement physique est primordial pour produire des produits qui seront acceptés par les organismes de réglementation – dans les produits pharmaceutiques, si les conditions ambiantes lors de la fabrication des médicaments ne sont pas étroitement contrôlées, l’ensemble du produit peut devoir être jeté. Le contrôle connecté et basé sur le cloud des équipements critiques permet aux fabricants de surveiller les indicateurs précoces indiquant que la température ambiante pourrait être affectée.
Dans les secteurs de haute technologie tels que la fabrication de semi-conducteurs ou de véhicules électriques, qui gèrent des opérations de fabrication massives, les technologies numériques et cloud constituent un énorme avantage concurrentiel pour maintenir les usines en activité 24 heures sur 24 et 7 jours sur 7, ce qui permet d’atteindre l’échelle nécessaire pour acheminer les produits vers le marché, en premier, un pilier de leur existence.
Pour répondre à ces changements, les grandes entreprises qui ont réussi à tirer parti de l’industrie 4.0 pour réaliser une transformation plus rapide et plus durable tirent parti de la technologie numérique pour créer des organisations plus agiles et axées sur le client. Cette approche permet aux fabricants de se concentrer sur l’amélioration de leur productivité, de la durabilité, de l’agilité, de la rapidité de mise sur le marché, de la personnalisation et de la satisfaction des clients, ce qui peut entraîner une augmentation tangible des revenus. Comment ça?
1. Les commandes connectées permettent d’obtenir de meilleures informations et d’améliorer les capacités de prise de décision
De nombreuses parties d’une installation de fabrication peuvent être mesurées : température, occupation, consommation d’énergie, inefficacités de l’équipement. Les capteurs connectés et intégrés dans l’ensemble d’une installation peuvent détecter des variations subtiles telles que les changements d’humidité relative et demander aux commandes du système d’ajuster les conditions ambiantes sans sacrifier l’efficacité ou risquer de s’écarter des points de consigne étroitement gérés.
Si la qualité de l’air intérieur (QAI) est préoccupante, les capteurs d’une installation peuvent indiquer si un espace est occupé et fournir la bonne quantité d’air extérieur pour augmenter le débit d’air. Les industries peuvent désormais tirer parti des technologies basées sur le cloud qui permettent un accès à distance sécurisé aux systèmes et processus critiques, et rendent la surveillance des systèmes plus immédiate, afin que des décisions puissent être prises rapidement pour résoudre les problèmes.
Grâce à des points de connexion dans toutes les parties d’une installation, les données sur le temps de fonctionnement, l’état des composants, la consommation d’énergie, etc., peuvent être analysées pour aider à améliorer l’efficacité de l’équipement CVC, à renforcer l’efficacité énergétique, à réduire les coûts et à atteindre les objectifs de durabilité.
2. Les services prédictifs utilisant les données, l’analyse, l’intelligence artificielle (IA) et l’apprentissage automatique (ML) permettent d’identifier les problèmes à un stade précoce
Une publication récente de McKinsey & Co estime que l’industrie 4.0 peut générer une valeur significative dans plusieurs domaines d’un réseau d’usines. Rien que pour les temps d’arrêt de la machine, une réduction de 30 à 50 % peut être réalisée. Et l’amélioration de la précision des prévisions peut atteindre 85 %. 1
L’utilisation de données et d’analyses qui maximisent les interactions homme-machine en tirant parti de l’intelligence artificielle (IA), des outils d’automatisation et de l’apprentissage automatique (ML) peut aider à identifier les problèmes opérationnels avant qu’ils ne surviennent et à éviter des temps d’arrêt coûteux. Par exemple, la mesure de la température interne des roulements à l’intérieur d’une unité de refroidissement peut indiquer si un refroidisseur est en bon état ou si une maintenance imminente sera nécessaire.
L’analyse prédictive peut également aider à générer des événements de maintenance planifiée moins chers, moins fréquents et de plus courte durée.
La connectivité combinée aux données, à la puissance de calcul et aux analyses avancées peut créer de la valeur tout au long de la chaîne de valeur de la production.
3. Les technologies numériques, comme l’utilisation de jumeaux numériques, permettent de modéliser des scénarios et de prédire le cycle de vie des produits ou la maintenance nécessaire.
Les technologies numériques, telles que l’utilisation de jumeaux numériques pour refléter un processus ou une installation, offrent la possibilité d’analyser de nombreuses variables de fonctionnement à la fois, puis de modéliser des scénarios de simulation qui peuvent aider à prédire les vulnérabilités d’un processus, les erreurs d’exécution, les contraintes d’équipement, etc. La surveillance et le diagnostic à distance qui utilisent des jumeaux numériques permettent également de repérer plus rapidement les défaillances potentielles, de sorte que les pièces de rechange critiques peuvent être à portée de main pour éviter des temps d’arrêt coûteux.
Essentiellement, avec les jumeaux numériques, les équipes peuvent se concentrer sur la résolution de problèmes qui font avancer une organisation plutôt que de passer du temps sur la manipulation manuelle des données.
Parlons de vos besoins de transformation
Trane peut vous guider dans une transformation numérique vers l’industrie 4.0 qui peut vous aider à améliorer le temps de disponibilité, à augmenter la fiabilité, à réduire les coûts et à atteindre les objectifs de décarbonisation et de durabilité. Nous adoptons une approche holistique pour vous aider à gérer votre voyage. Notre approche Wayform combine les conseils fiables des professionnels de Trane avec des données et des informations sur les bâtiments pour aider les fabricants industriels à utiliser l’énergie plus intelligemment et à réduire les émissions de carbone. Nous travaillons avec nos clients tout au long du processus de planification, de mise en œuvre et de service continu. Nous produisons des équipements durables et de haute qualité ; offrir une expertise en matière de personnalisation des systèmes et d’applications ; se concentrer sur des services intelligents pour minimiser les coûts ; et fournir une expertise approfondie de l’industrie et du domaine. Entamons une conversation.
1 Saisir la vraie valeur de l’industrie 4.0, 13 avril 2022, McKinsey & Co